Screw feeder DRS-G
with inlet hopper 450 x 300 mm
Dosing screws type DRS-G are developed for dosing of powders and granulates. The dosing capacity is between 9 and 51,000 l/h depending on the size.
Our proven modular system for dosing screws meets most requirements for dosing of powders and granulates.
They are made of stainless steel 1.4301 (V2A, AISI304) and are easy to clean.
If you have customization requests, we would like to consider them.
We would be pleased to talk about the task with you.
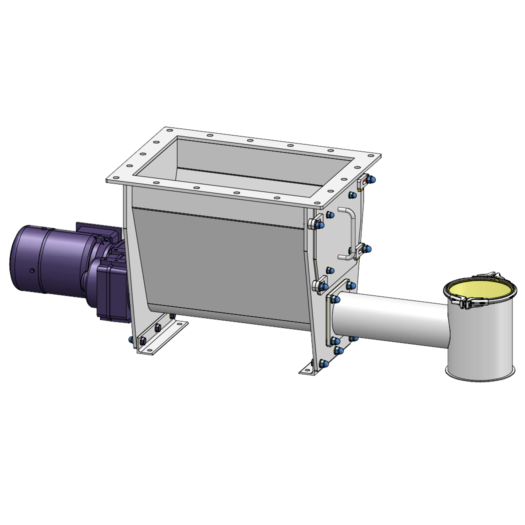
Screw feeder DRS-GBasic design
- Parts in contact with the product are made of stainless steel AISI 304
Sealings in contact with the product are food compatible according to 1935/2004/EG and FDA - Designed for biologically dry food and dry cleaning
- Cleaning hatch at the front plate, dosing tube dismountable
- Surfaces
outside - pickled and glass bead blasted
inside - welding seams grinded and pickled - Screw feeder with geared motor with temperature sensor for onsite frequency converter
- Progressiv thread pitch in the inlet area
- Transparent lid above the outlet or aspiration connection
- Prepared for installation of a dispersing agitator
Basic configuration
- Design for use in the EU
- Inlet hopper with app. 20 l capacity
- Prepared for installation of a dispersing agitator
- Cleaning hatch at the front plate
- Screw shaft mounted on one side
- Screw shaft screwed in and easy to change
- Progressive thread pitch in the inlet area
- Double screw blade at the outlet for more exact dosing
- Shaft mounted geared motor in on-slip design
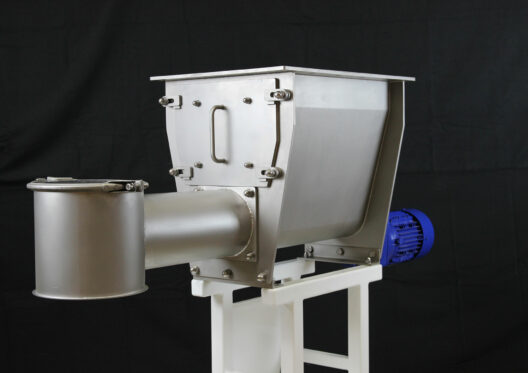
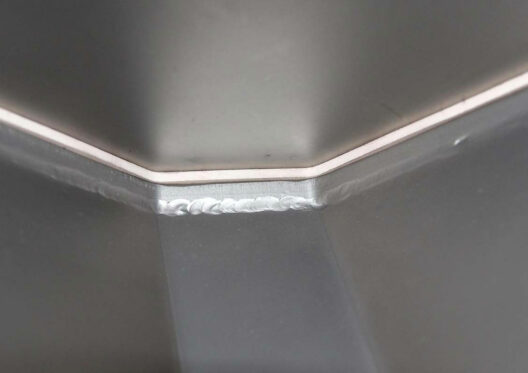
Material and surfaces
Stainless steel AISI 304
Surfaces
Outside pickled and glass bead blasted
Inside surfaces 2B, welding seams grinded and pickled
Optional: Surfaces in contact with product Ra<0,8 µm welds Ra<1,6 µm
Defects in the surface can occur
Flat sealings
Flat sealings for flanges and hatches are made of white NBR for food according to 1935/2004/EG and FDA.
Geared motor
- Shaft mounted geared motor make Nord type SK0282
- On-slip design
- Voltage 230/400 V, 50 Hz
- Protection class IP55, insulation class F
- Temperature sensor TF for thermal motor protection. Thermistor 3 x 155 °C
- Nord standard painting RAL 7031 blue-gray
Gear oil:
- for Non-Food: Mineral oil CPL 220
- for food: synthetic gear oil CLP PG H1 220 (FDA 178.3570)
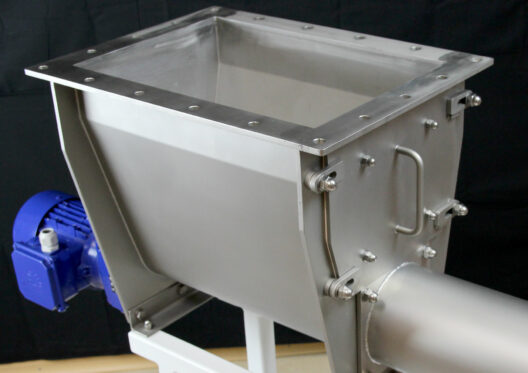
Inlet
The inlet is designed as an inlet hopper 450 x 300 mm.
As standard accessories we offer optional:
- Loose counter flange
- Hopper 50 l usable volume, inclination 90°, height 400 mm
- Hopper 100 l usable volume, inclination 90°, height 800 mm
- Hopper 200 l usable volume, inclination 90°/ 72° / 66°, height 800 mm
- Hopper 500 l usable volume, inclination 90°/ 72° / 66°, height 1300 mm
Hopper (option)
The corners are bended 2x 45° in order to minimize the sedimentation of product and to facilitate cleaning.
Surfaces outside glass beads blasted. Surfaces inside are 2B.
The cover is screwed on and has an inlet Ø150 mm for Jacob pullring, a connecting flange Ø100 mm for Jacob pullring and an inspection opening with rubber cover.
Two windows made of Polycarbonat (PC for food according to 1935/2004/EG and FDA) are integrated into the vertical sides. The windows are flush with the inner wall.
Optionally we offer limit switches (full / empty) which are mounted on adjustable brackets in front of the windows. For light products and products that adhere to the windows, the limit switches may not be suitable.
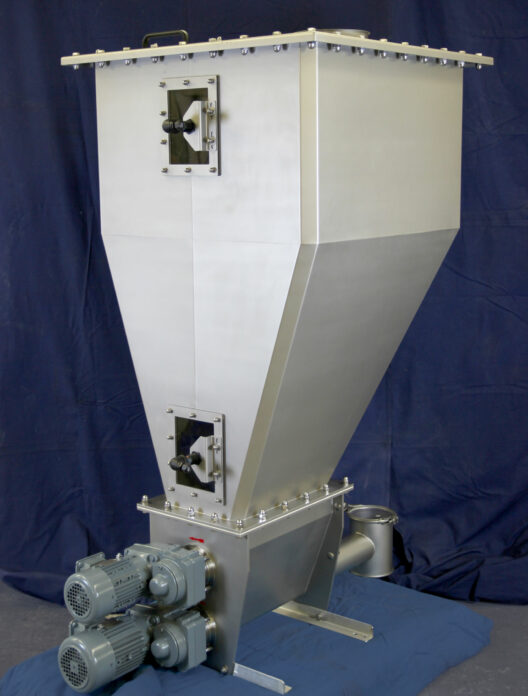

Outlet
Our standard outlet connections are:
- for Jacob pullring
- Jacob loose flange
- Fixed flange PN10
- Outlet for mounting a hose
- Horizontal outlet (without vertical outlet tube)
On demand we manufacture the outlet according to your specifications.
Pneumatic shutter stamp (option)
The pneumatic shutter stamp prevents trickling when the dosing process is complete.
The stamp is made of silicone and suitable for food.
With 5/2-way magnetic valve with one coil 24 V or 230 V
With 2 limit switches
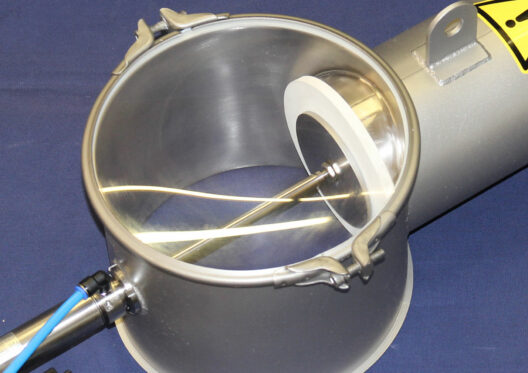
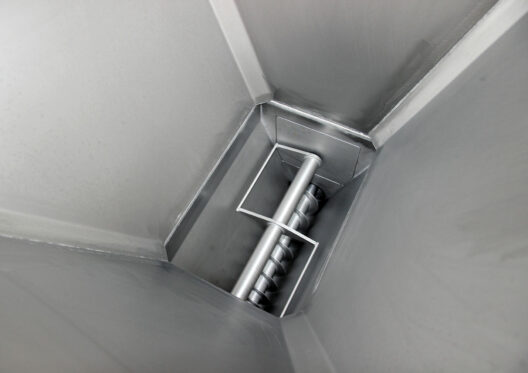
Dispersing agitator (option)
The dispersing agitator can reduce bridging and improves the dosing accuracy for products which are not free-flowing.
Geared motor 0.37 kW, 24 rpm. Design is the same as the geared motor of the screw.
The dispersing agitator can be ordered at a later time and can be installed by a fitter of the plant because the hopper is prepared for this.
Lump breaker (option)
The lump breaker can crush easily breakable lumps so that they can be better conveyed and dosed. It is not suitable for hard lumps.
We can test the use with your product, if you send us an product sample of at least 10 liters.
Gap width is 18 mm.
Geared motor 0.37 kW, 24 rpm. Design is the same as the geared motor of the screw.
The lump breaker can be ordered at a later time and can be installed by a fitter of the plant because the hopper is prepared for this.
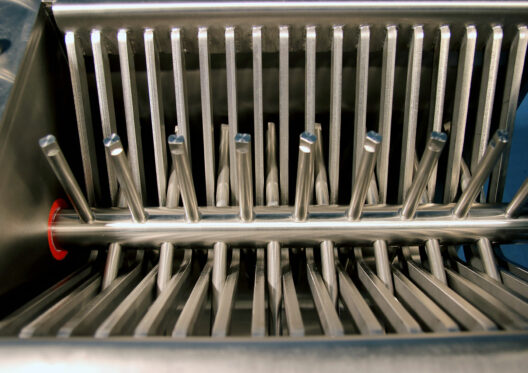
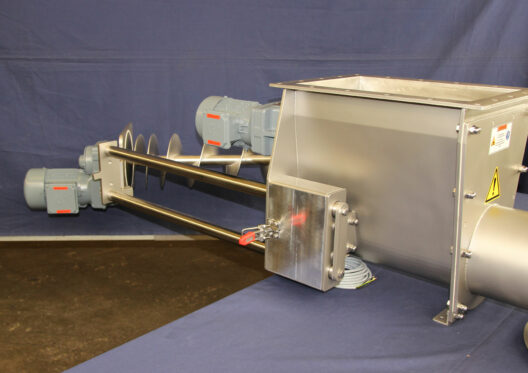
Thread pull-out device (option)
The thread pull-out device enables quick and effective cleaning.
The screw shaft should not be longer than 1000 mm. That means middle inlet to middle outlet is maximum app. 800 mm
With safety switch for the thread pull-out device. An evaluation device is neccessary, we can offer separately.
The thread pull-out device must be ordered with the basic configuration. It cannot be retrofitted at a later time.
The standard design of the thread pull-out device is for dry and non-sticky products. For humid environment and sticky products we offer on request an alternative design of the thread pull-out device.
Screw feeder sizes and technical data
Geared motor | Rated capacity l/h at 50 Hz Calculated capacity l/h at 5 Hz - 85 Hz at 100% filling |
|||||||||||
rpm | DRS060 | DRS100 | DRS150 | |||||||||
---|---|---|---|---|---|---|---|---|---|---|---|---|
32 rpm | 85 l/h 9-145 l/h |
0.55 kW | 566 l/h 57-963 l/h |
0.55 kW | 2697 l/h 270-4584 l/h |
0.55 kW | ||||||
47 rpm | 125 l/h 13-213 l/h |
0.55 kW | 832 l/h 83-1414 l/h |
0.55 kW | 3961 l/h 396-6.733 l/h |
0.55 kW | ||||||
66 rpm | 176 l/h 18-299 l/h |
0.75 kW | 1168 l/h 117-1986 l/h |
0.75 kW | 5562 l/h 556-9455 l/h |
0.75 kW | ||||||
85 rpm | 277 l/h 23-386 l/h |
0.75 kW | 1504 l/h 150-2557 l/h |
0.75 kW | 7163 l/h 716-12177 l/h |
0.75 kW | ||||||
109 rpm | 291 l/h 29-494 l/h |
0.75 kW | 1929 l/h 193-3279 l/h |
0.75 kW | 9185 l/h 919-15615 l/h |
0.75 kW | ||||||
129 rpm | 344 l/h 34-585 l/h |
0.75 kW | 2283 l/h 228-3881 l/h |
0.75 kW | 10871 l/h 1087-18480 l/h |
0.75 kW | ||||||
161 rpm | 430 l/h 43-730 l/h |
0.75 kW | 2849 l/h 285-4844 l/h |
0.75 kW | 13567 l/h 1357-23065 l/h |
1.1 kW | ||||||
190 rpm | 507 l/h 51-862 l/h |
0.75 kW | 3362 l/h 336-5716 l/h |
0.75 kW | 16011 l/h 1601-27219 l/h |
1.1 kW | ||||||
236 rpm | 630 l/h 63-1071 l/h |
0.75 kW | 4176 l/h 418-7100 l/h |
0.75 kW | 19888 l/h 1989-33809 l/h |
1.1 kW | ||||||
264 rpm | 704 l/h 70-1198 l/h |
0.75 kW | 4672 l/h 467-7942 l/h |
1.1 kW | 22247 l/h 2225-37820 l/h |
1.1 kW | ||||||
Lighter blue fields: Peripheral speed more than 1.0 m/s at 75 Hz. With explosive products only permitted under certain conditions |
Screw feeder DRS-G design and accessories
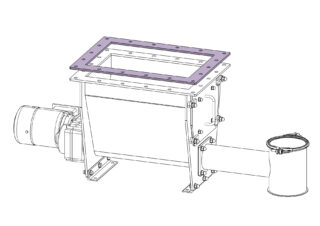
Loose counter flange
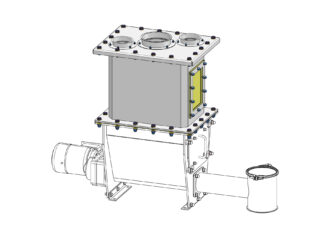
Hopper 50 l
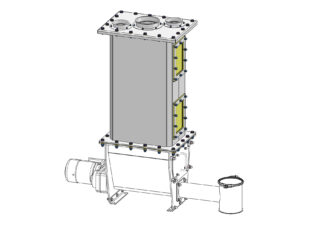
Hopper 100 l
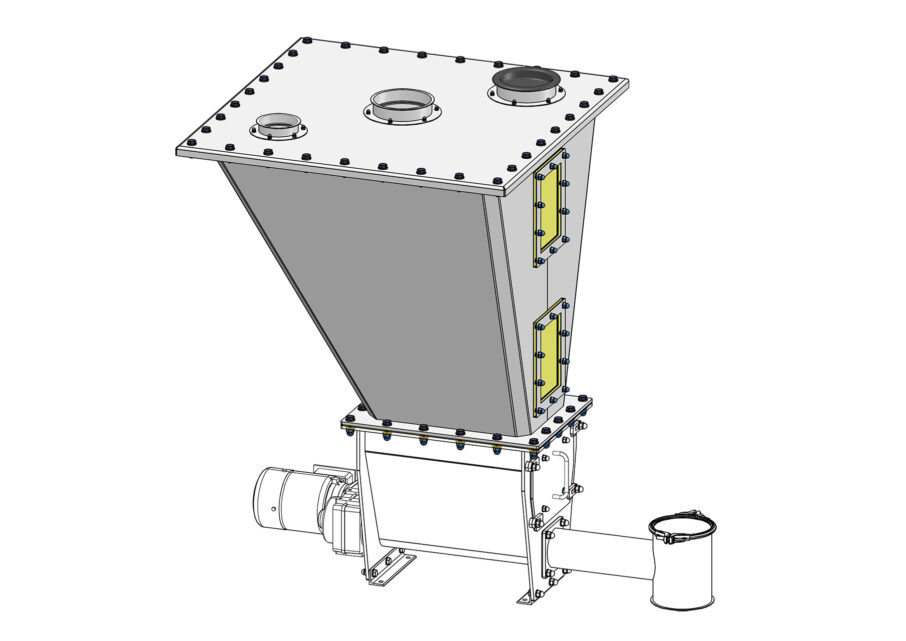
Hopper 200 l
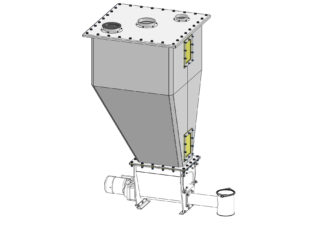
Hopper 500 l
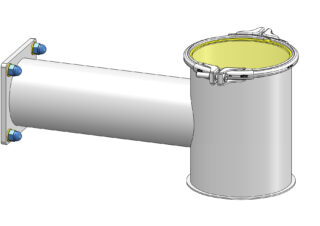
Outlet for JACOB pullring
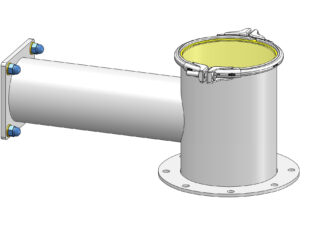
Outlet with JACOB loose flange
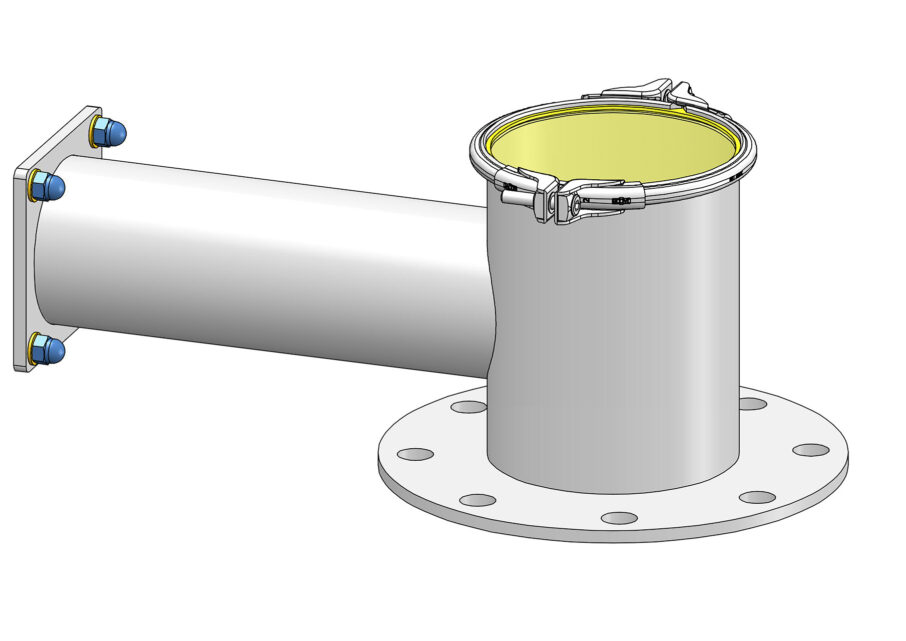
Outlet with fixed flange PN10
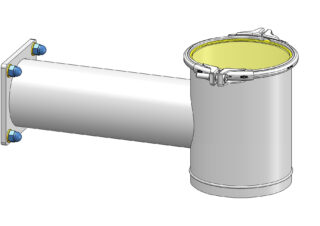
Outlet for mounting a hose
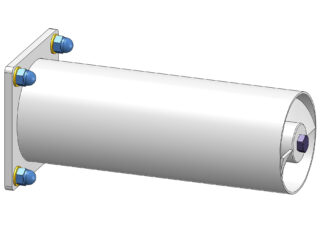
Horizontal outlet
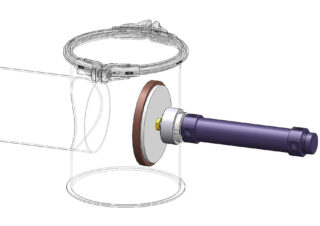
Outlet with shutter stamp
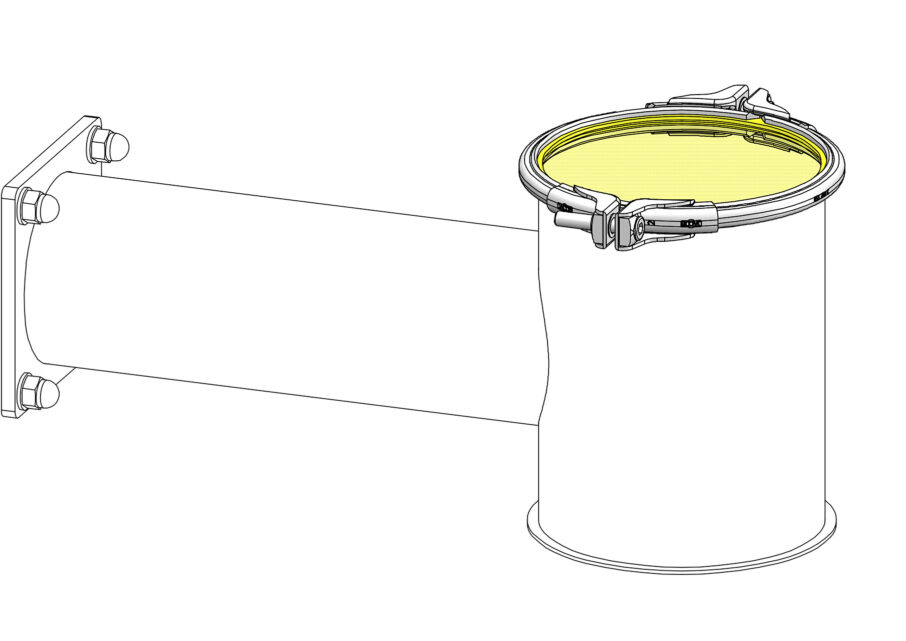
Transparent lid above outlet
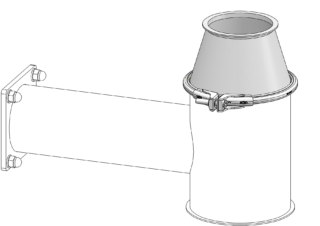
Connection for aspiration Ø100 mm JACOB lip flange
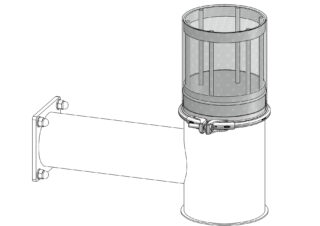
Outlet with filter cage
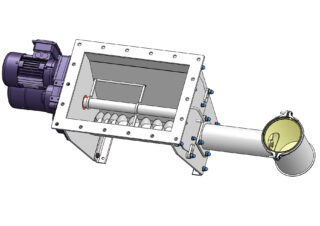
Dispersing agitator
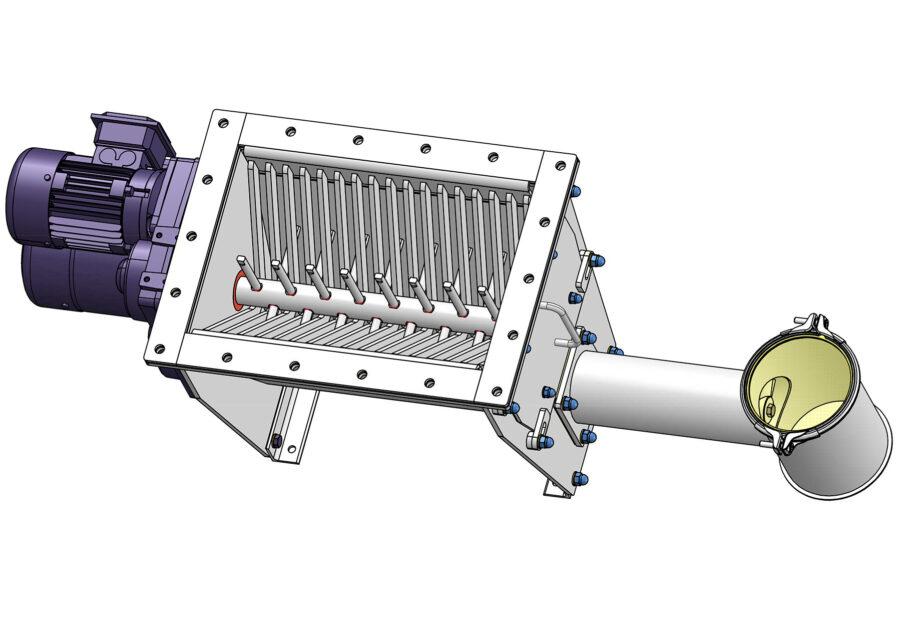
Lump breaker
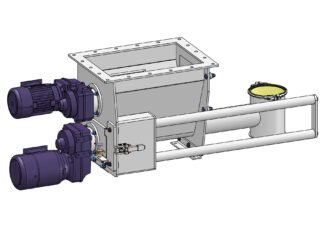
Screw feeder DRS-G with thread pull-out device
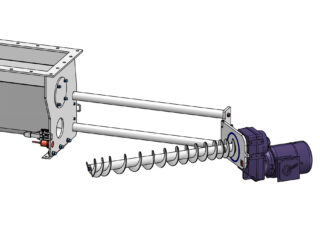
Thread pulled out
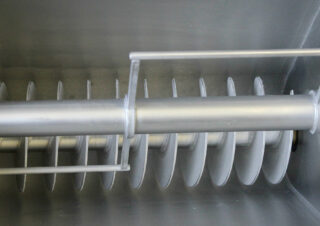
Inner surfaces 2B, welding seams grinded and pickled
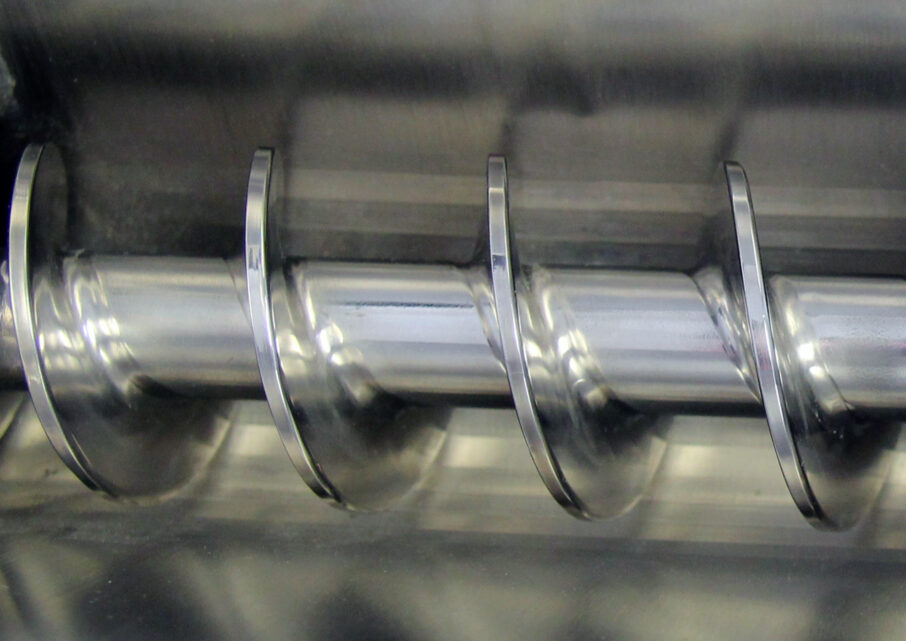
Inner surfaces RA<0.8 μm, welds <1.6 μm
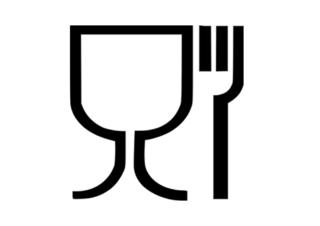
Design for dry food
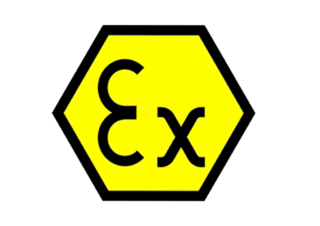
Design for ATEX areas (zone 22 and 21)
Shaft sealing
The shaft sealing is mounted into the flange of the gear motor. This flange is designed so that different shaft sealings can be installed.
In addition to the standard shaft seal, a special shaft seal can be installed for other temperature ranges.
The shaft sealing can be exchanged with another shaft sealing by a service fitter at a later time, if this is required e.g. by product change.
- Standard shaft sealing with shaft sealing ring
- Optional shaft sealing DynamicSeal with flushing air
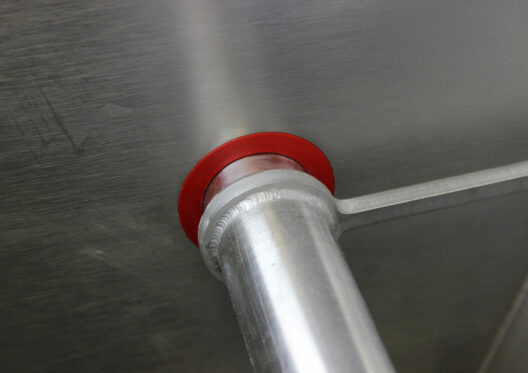
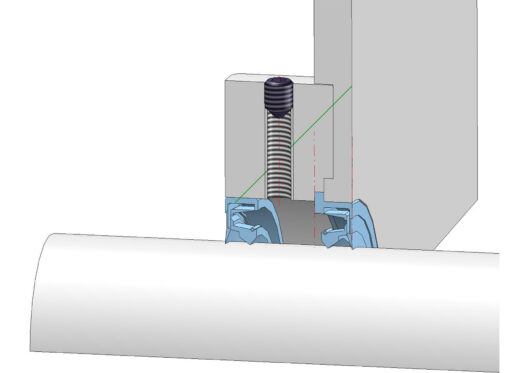
Standard shaft sealing
Shaft sealing ring made of Polyurethan, support made of POM and spiral spring made of stainless steel.
For food according to 1935/2004/EG and FDA
Operating temperature -20 to +100 C
Resistant to: Oil up to 60 C, grease, dilute acid, dilute alkalis, water up to 90 °C
Not resistant to concentrated acids and concentrated alkalis.
Shaft sealing DynamicSeal with flushing air
Sealing ring made of PTFE for food according to 1935/2004/EG and FDA
connection for compressed air with hose connection outside Ø6 mm
Compressed air consumption app. 12.5 Nl/min
compressed air min 0.1 bar
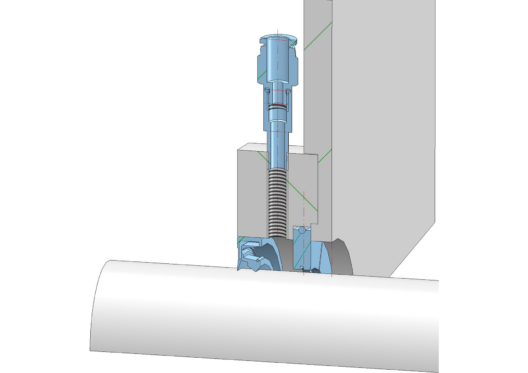
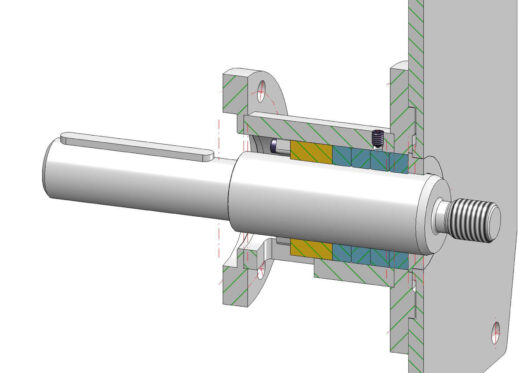
Shaft sealing with stuffing box
- Adjustable
- Packings also for contact with food
- Optionally with flushing air
Dimension drawing for screw feeder DRS-G
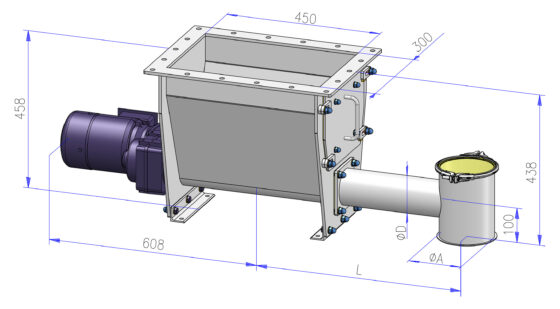
Dimensions of screw feeder DRS-G
Type | dosing tube Ø | outlet Ø | ||||
---|---|---|---|---|---|---|
DRS060G | 60 mm | 120 mm | ||||
DRS100G | 103 mm | 150 mm | ||||
DRS150G | 153 mm | 200 mm | ||||
L possible from 450 mm up to 900 mm |
How to contact us
Phone +49 4121-7957-0
Fax +49 4121-7957-79
eMail e-mail@paul-groth.com
Contact us
Use the contact form or email, and the right employee will contact you directly.
Tags: DischargeDosageDosing devicesDosing screwsScrew feederTubular screw conveyors